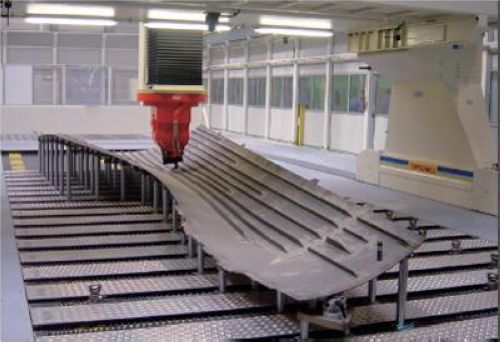
From the above data, we can see that since the impact of the global economic crisis last year, China has not fully recovered this year. As analyst Luo Baihui said, industry demand is still weak and the situation is still low, but it is down compared with last year. The trend has gradually eased.
So, what is the development of other countries or regions that are also deeply affected by the economic crisis? From the following sets of data can be glimpsed.
According to statistics from the American Manufacturing Technology Association, from January to May 2013, the US orders for metal processing machine tools were US$2.09 billion, a decrease of 6.9% year-on-year. Among them, orders for metal cutting machine tools were 1.87 billion U.S. dollars, down 7.7% year-on-year; orders for forming machine tools were 210 million U.S. dollars, up 0.2% year-on-year.
In Japan, according to the statistics of the Japan Machine Tool Industry Association, in the first half of 2013, the total orders of eight major machine tool manufacturers in Japan were 219.43 billion yen, a year-on-year decrease of 17.1%. The eight machine tool manufacturers include Mori Seiki Co., Ltd., OKUMA, Makino Manufacturing Co., Ltd., Osaka Kogyo OKK, Toshiba Machine Co., Ltd., Jinshang Jietete, Toyota Mechanic, and Mitsubishi Heavy Industries.
According to statistics, the eight domestic machine tool manufacturers needed orders for 74.22 billion yen in the first half of the year, a decrease of 21.1% year-on-year, and orders for external demand were 145.21 billion yen, a decrease of 15.0% year-on-year. The proportion of foreign demand increased by 1.7 percentage points to 66.2%.
It is not difficult to see that the situation of the machine tool industry in the United States and Japan is similar to that in China. In Luo Baihui's view, "Compared with ten years ago, the level of China's CNC machine tools has increased a lot." Ten years ago, China could not produce five-axis linkage machine tools, and now there are several domestic brands. The price of similar products in Japan has been forced to drop sharply. Some other heavy-duty machine tools have reached the international advanced level, and domestic five-axis machine tools are also a landmark achievement.
The remarkable progress in the level of machine tools in recent years has enabled us to achieve breakthroughs in some manufacturing sectors. However, we still have not mastered production technologies for some important high-end CNC equipment. This has caused us to be constrained in some of the most important manufacturing sectors such as large aircraft and integrated circuit manufacturing. Therefore, to achieve a full-scale manufacturing industry, high-end numerical control equipment still has to overcome difficulties.
"We are still following the advanced technology (valves, pumps)." Luo Baihui believes that China's CNC machine tools still have a gap in terms of speed and precision. The same specifications of the product, foreign machine tool speed is probably three times the domestic machine tools, accuracy is also close to an order of magnitude higher.
CNC machine tools are a very complex industry in the production process. The technical bottleneck of domestic machine tools is hard to attribute to a single specific link. In general, CNC machine tools consist of digital control systems and machine tools. China has a gap between these two aspects.
On the one hand, high-performance CNC systems are the key factors that determine the performance and cost of the entire machine. The domestic high-end CNC machine tools exhibited at this year's Nanjing Expo use CNC systems from foreign companies such as Siemens or Fanuc. The domestic CNC system has obvious gaps from the advanced world level in terms of high-speed, high-precision, five-axis processing and intelligent functions. This is due to the difference in the architecture of the domestic CNC system (hardware platform, software platform, field bus), high-speed and high-precision control algorithms, and servo drive. On the other hand, functional components such as electric spindles, double-swinging heads, turntables, and nano-precision gratings, as well as the core technologies for the design and manufacture of complete machines, are also key constraints for manufacturing high-end machine tools in China. The improvement of the overall technology of CNC machine tools in China is ultimately inseparable from the support of advanced functional component industries.
The huge demand for domestic markets (machine tools, valves, and pumps) is an active factor in driving technological progress. It can be expected that by 2020, high-end CNC machine tools needed in various fields of manufacturing will have a large number of products produced in China.
Ninja Obstacle Course,Ninja Slackline,Ninja Slackline Course,Ninja Slack Line
Taizhou Gentle Booms Outdoor Products Co.,Ltd , https://www.gentleboomssports.com